|
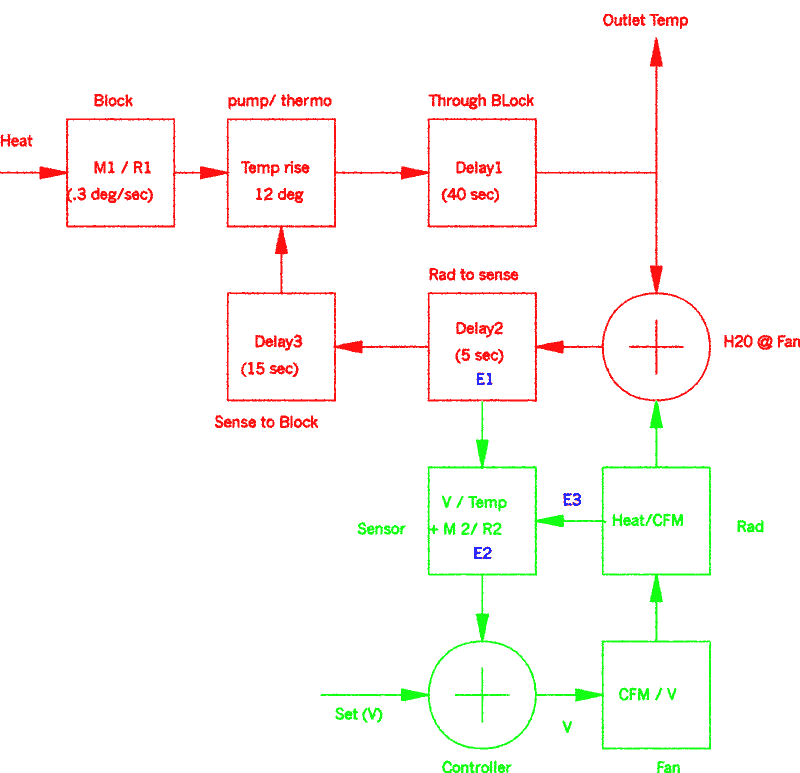
The diagram
above shows the operation of the FK series controllers. The mechanical related
components are shown in red and the controller related components are shown in
green.
From the left,
the heat of combustion enters the block byway of the combustion medium., the
thermal resistance of the mixture provides a slow rise in temperature on the
order of .3 degrees per second. The coolant flows through the block in order to
scavenge heat to be transferred to the radiator, as the temperature of the coolant
moves through the
block its temperature rise is influenced by the flow rate of the coolant, the heat capacity of
the coolant, and the heat generated. An underdrive pulley set will increase the
temperature rise by about 4 degrees, as will a high mixture of antifreeze. With the
combination of the two, a one step lower temperature setting of the controller will offset any
deviation from the 12 degree rise. It should also be noted that a closed
thermostat will also increase the temperature rise.
The coolant
takes approximately 40 seconds to travel through the block and to the radiator
before the heat is transferred to the radiator where the heat is removed from
the system. The heat is removed from the coolant byway of the radiator and
fan and another, much shorter delay occurs before the temperature is sensed.
Finally, a third delay, from the radiator to the block occurs and then the cycle
repeats. The sensor measures the temperature of the coolant at the radiator
output and converts the temperature to a tracking voltage; the controller then
compares this voltage to the set voltage (jumpers), and outputs a control
voltage to the cooling fan that is proportional to the difference in these
voltages. Finally, the fan pulls that heat from the radiator in order to keep
the coolant at the set temperature. Because the temperature rise through the
engine is constant, a 12 degree sensing offset at the controller keeps the
engine outlet temperature at the controller set point.
The delay from
the coolant at the fan to the coolant at the probe causes a delay in the
reaction time of the controller. This error, E1, is significantly small, given
that the rise in temperature is only .3 degrees per second. Although this would
appear to provide a 1.5 degree overshoot in temperature, the error occurs at the
bottom of the ramp up of the controller, which is typically three degrees lower
than the running temperature, so no overshoot occurs. Even with a 25% decrease
in the rate of coolant flow, which is typical when using underdrive pulleys, the
overshoot is only 2 degrees, which is still lower than the three degrees
mentioned earlier.
A second error,
E2 will occur if the probe is not well thermally coupled to the radiator.
Placing the sensor from the front of the radiator will also cause this problem
when slowing from freeway speeds, due to the fact that the probe and the most
forward radiator fins will be cooled far below the coolant temperature from the
airflow. When the car comes to a stop, the probe temperature needs to rise from
ambient to the coolant temperature, which takes time and causes a temperature
overshoot, so the sensor should always be placed on the engine side of the
radiator
Finally, a third
error E3 occurs if the probe is cooled directly by the fan. The result of this
error is a decrease in the loop gain of the system, in that the full-off to
full-on temperature range will increase. Placing the sensor towards the corner
of the radiator, however, renders this error insignificant.
Setting the
temperature lower than that of the mechanical thermostat will cause the
thermostat to close and will result in an increase in the time delay (E1)
significantly enough to cause a delay in the starting of the fan and a
subsequent overshoot in the fan speed and although this will effect the
temperature stability to some degree by causing the thermostat to cycle, the
main effect will be an increase in the perceived fan noise. A second order
temperature variance will also result byway of the hysteresis of the mechanical
thermostat.
Because the
design results in very low measurement errors, a very stable engine temperature,
void of any heat cycling with a full-off to full-on variance of only seven
degrees is typical.
|
|